Subteams
Rider Development
The Rider Development subteam focuses on maximising the performance of the rider. Composed of both riders and technical members, this subteam arranges cycling and strength training for the riders and constructs personal rider power plans. They organise competency training to ride the recumbent bikes and physically test its mechanical and electrical systems. The Rider Development subteam is also in charge of organising and coordinating testing days at the Holden and Ford Proving Grounds.
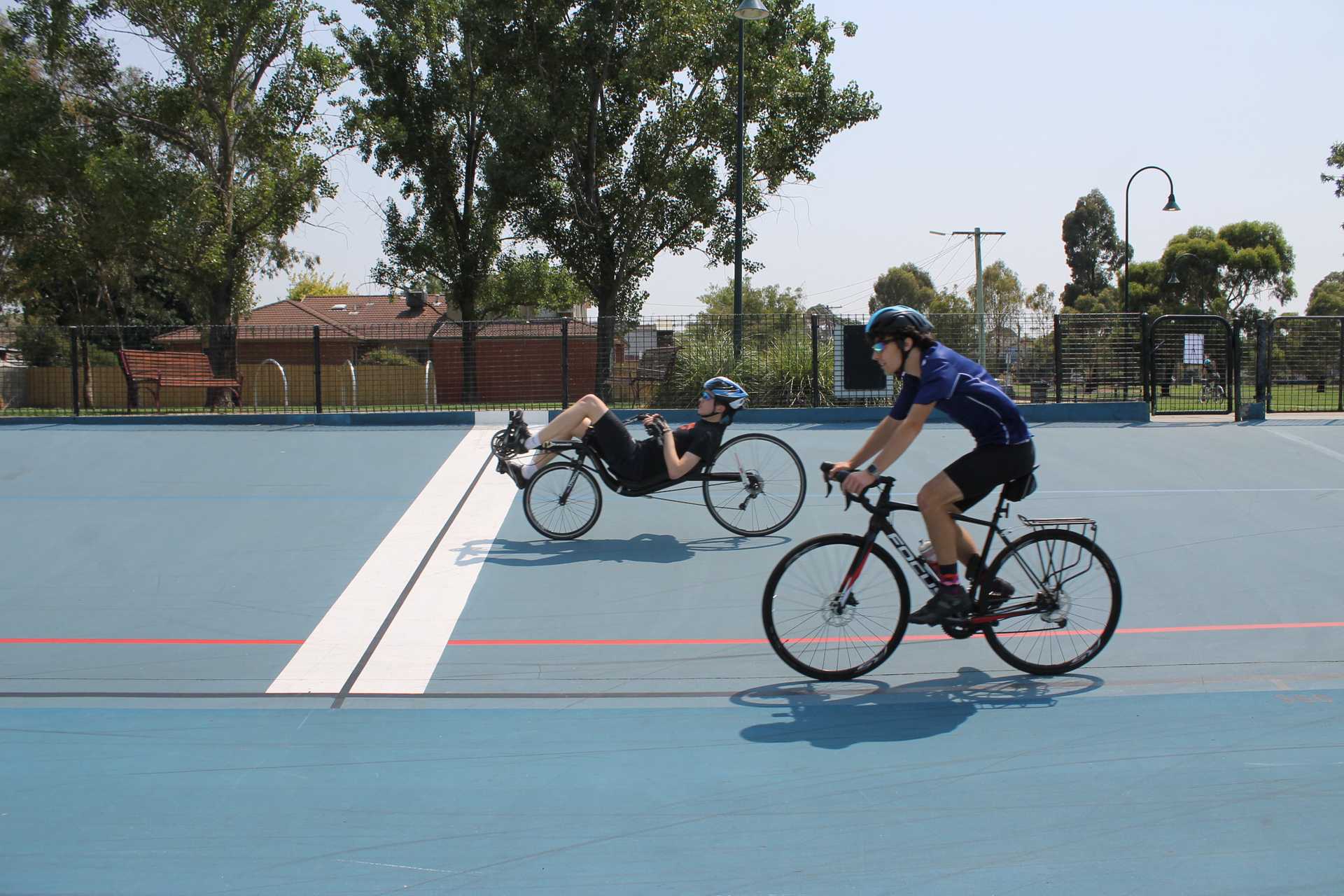
Aerodynamics
The Aerodynamics subteam at MHP is chiefly responsible for the design and testing of the aerodynamic components of the bike, such as the external shell and wheel covers. The key purpose of the external shell (also referred to as the 'fairing') is to reduce drag on the bike. This means that it is designed to optimise the airflow to increase the maximum speed that the bike can reach. Through the use of computational fluid dynamics (CFD), as well as experimental testing in the Monash Wind Tunnel, the team is able to make aerodynamic design choices that can significantly improve the performance of the bike.
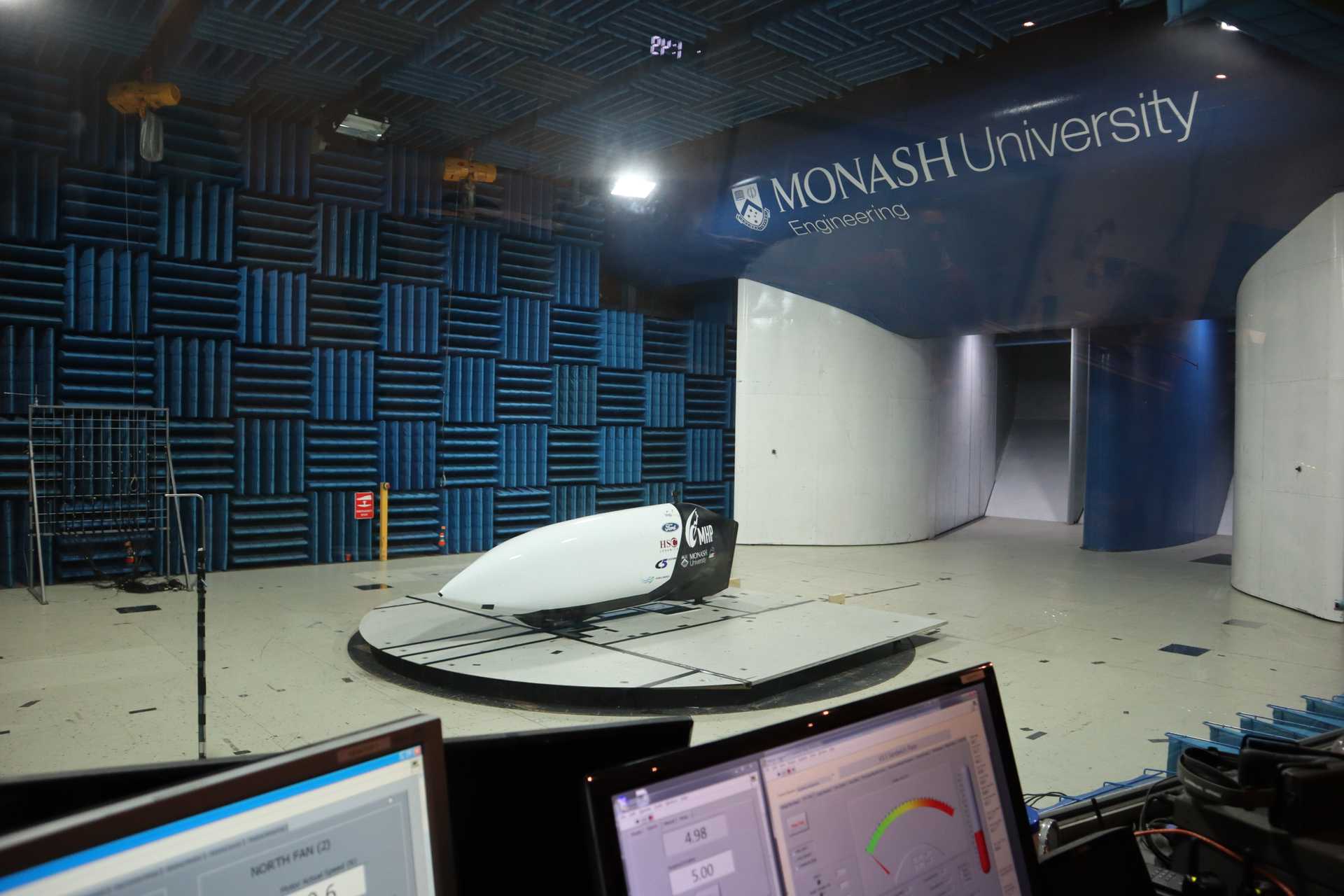
Chassis & Drive-train
The Chassis & Drive-train subteam is responsible for the design and manufacture of all mechanical components on the vehicle. This includes the structural frame (referred to as the chassis) and the moving parts of the vehicle. The design process involves modelling components through the use of CAD software, and then verifying that they are capable of withstanding the relevant loading through testing on FEA software or through hand calculations. The subteam utilises the resources available at Monash University to create the components, using manufacturing techniques such as welding, grinding, drilling and turning.
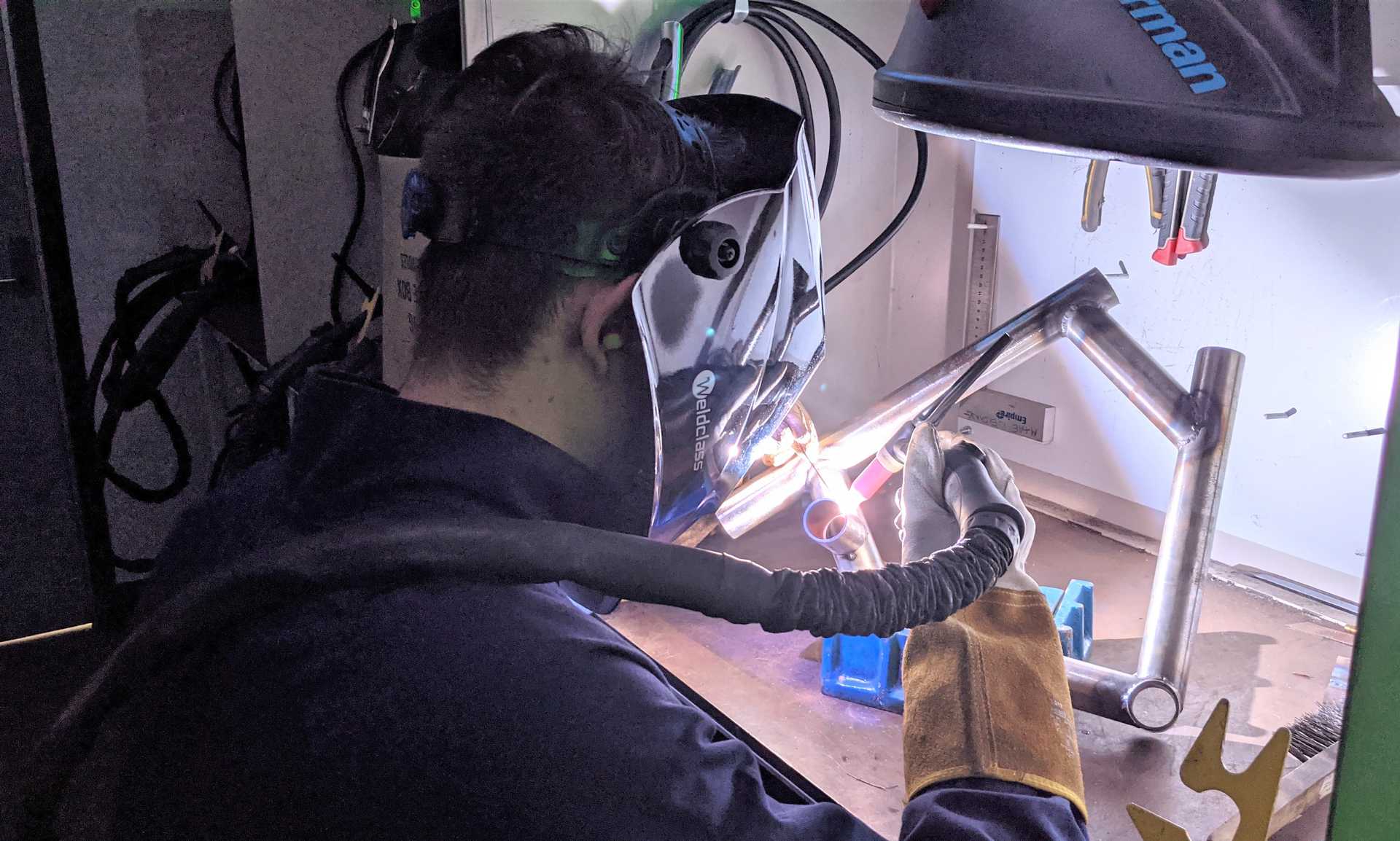
Operations
The Operations subteam identifies and engages external stakeholders to effectively facilitate the operations of MHP. This includes coordinating with sponsors and marketing MHP activities. They are also in charge of organising events to promote the missions of MHP, such as our flagship 'Build a HPV' school outreach program which encourages STEM pathways and educates students on sustainable transport. The Operations subteam also provides support to the technical side of MHP and their endeavours to efficiently manufacture the bike. Members of the operations subteam are also highly involved in the graphic design and branding of MHP.
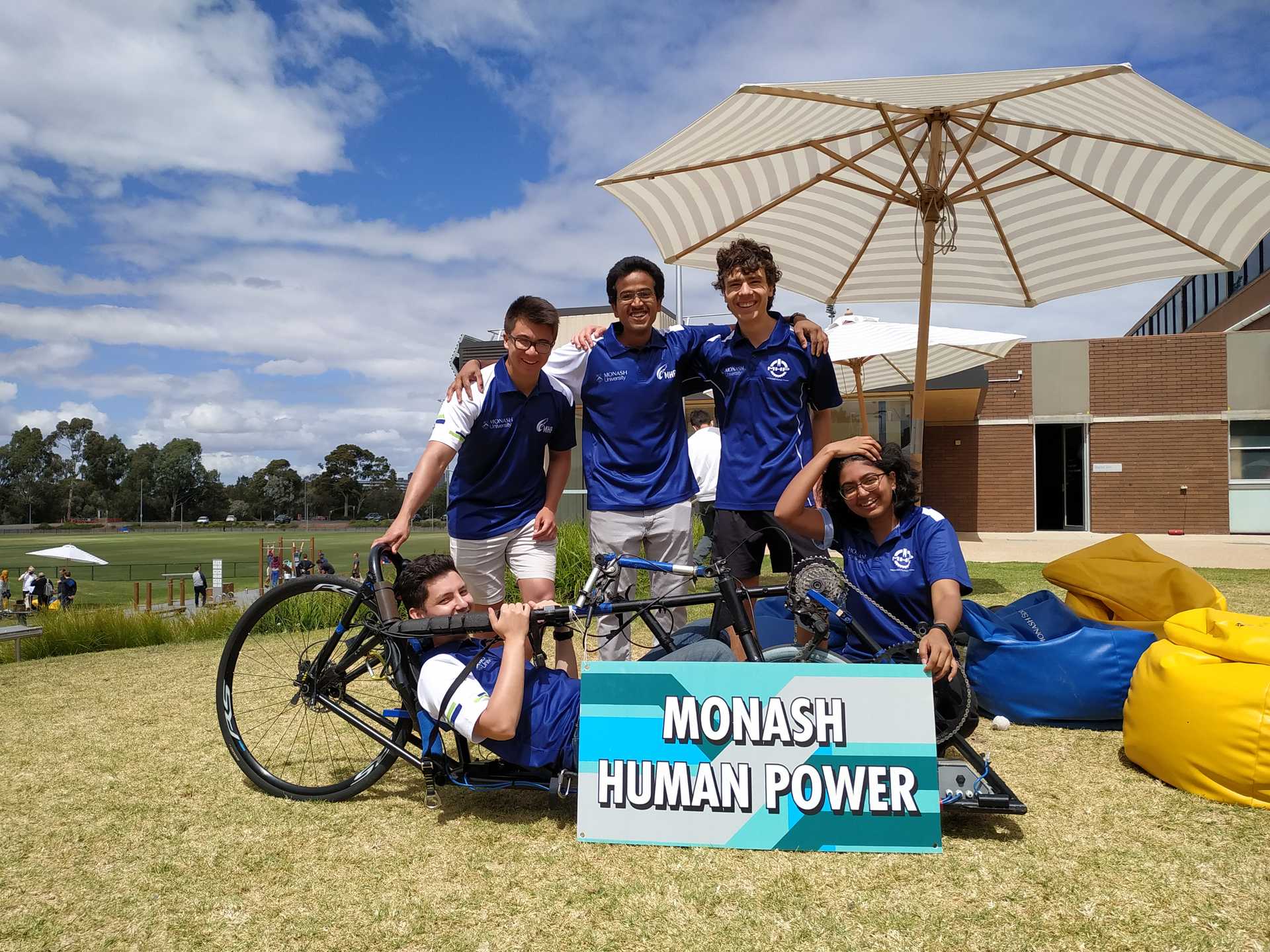
Electrical
The Electrical subteam handles both the electrical and software aspects of the bike. They design the camera and data acquisition system to improve the rider's safety and performance. There are no windows on the fairing, so the rider relies on this camera system to display the bikes surroundings and other information during the run. The systems consist of Raspberry Pis, microcontrollers, and a network of sensors. They also create custom software to record data from field testing, which later is used to review and analyse the performance of the bike.
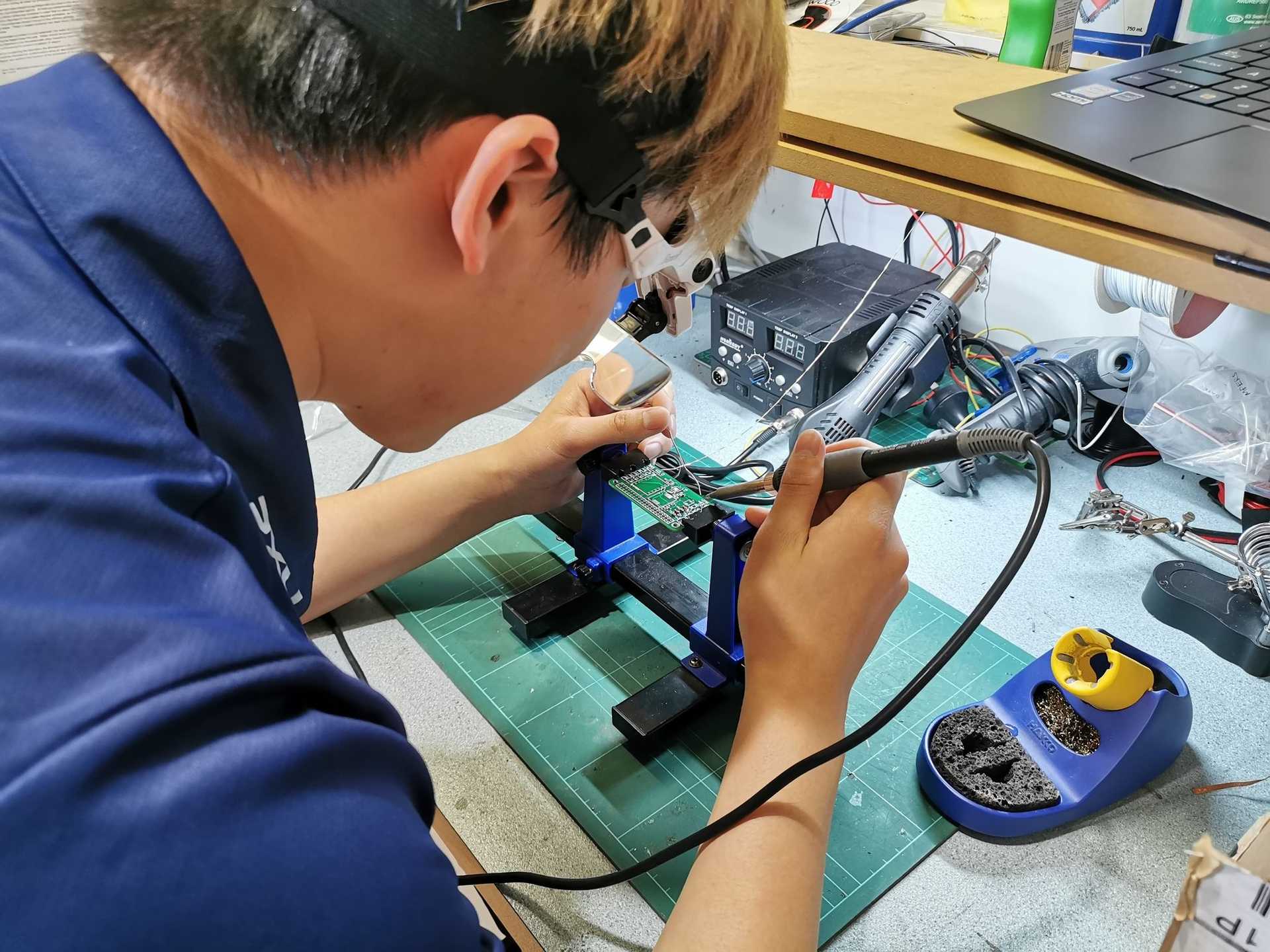
Materials
The primary purpose of the Materials subteam is to prototype and manufacture the fairing. This includes undergoing a design process to test and optimise the quality of the fairing to ensure the aerodynamic performance of the bike and rider safety. They also carry out extensive research to find the most viable methods and materials to produce the fairing. Currently, the fairing is fabricated using a resin infusion technique, which uses epoxy resin and carbon fibre. The Materials subteam uses power tools, applies surface finishing processes and creates composite components in order to produce the fairing.
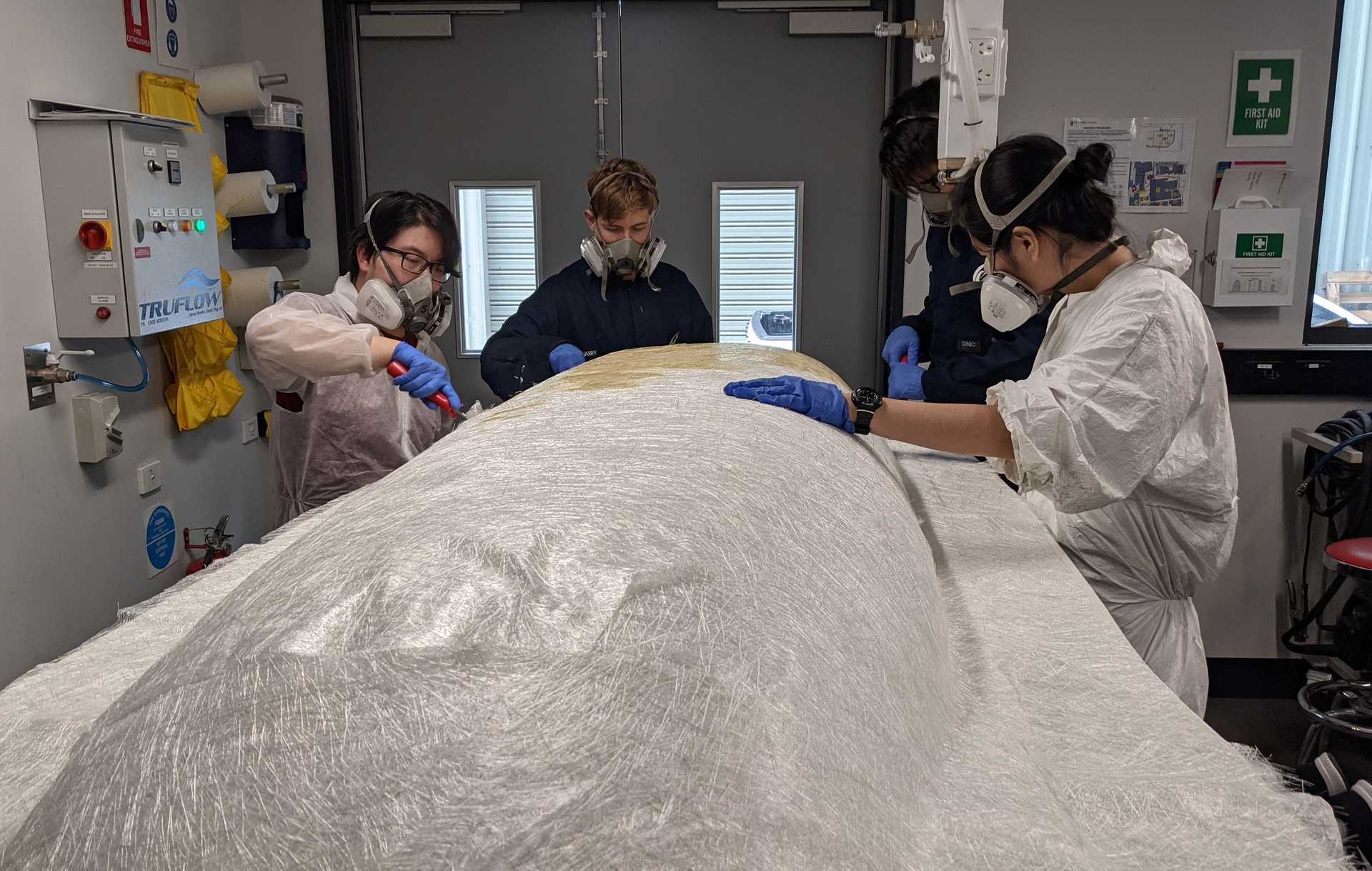